What is surface treatment?
CNC Machining
CNC Turning
Swiss Type CNC Machining
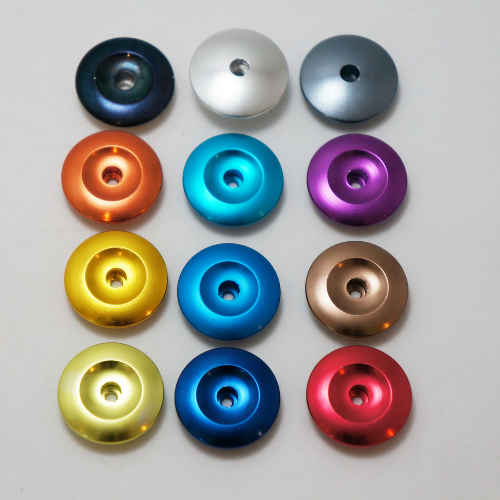
Finishing
The workpiece surface effect obtained by directly treating the workpiece with all types of machinery and equipment without any post-processing is known as the machined surface. The surface quality of workpieces is improving all the time as contemporary equipment become more precise. Although machining lines can be observed on the workpiece surface, it is actually quite smooth, with a Ra3.2 overall machined surface quality.
Polishing is a technique that involves grinding and altering the surface of an item with a variety of instruments and substances. Polishing has the effect of making the surface of the part more smooth and shiny, but it has no effect on the geometric shape or dimensional correctness of the part. Polishing is the process of using abrasives and machines to smooth the surface of a loose part, and using machinery to apply abrasives to a loose part surface is a more positive procedure that results in a smoother and brighter surface finish.
On mechanical parts, polishing is usually divided into three steps:
-The first step is to polish the component surface with an oilstone since it is generally rough after the scar, mill, NC, spark machine, wire cutting, and other processes.
-The second phase is sandpaper work, which should be done after the oilstone operation. When sandpapering, we should focus on the sections of the round edge, sharp corner position, fillet, and orange peel creation.
-The third step: With precise requirements of Ra0.2, we mostly employ diamond grinding paste, which necessitates a clean polishing environment.
Common anodizing and hard anodizing are the two types of anodizing.
Metal anodizing is the electrochemical treatment of metal surfaces to generate a conversion film with wear resistance, corrosion resistance, and other functional or ornamental features, with the treated components as the positive pole and the corrosion-resistant material as the negative pole.
Aluminum and aluminum alloys, magnesium alloys, titanium and titanium alloys, and other metals and alloys can be anodized. Aluminum and aluminum alloy anodizing is an extensively used and rapidly developing market.
The main purpose of anodizing is to increase the workpiece’s hardness, wear resistance, corrosion resistance, and surface coloring, which helps to protect and beautify the surface.
Sandblasting is a post-treatment method that uses high-pressure air to spray abrasives into work that need surface treatment at a high rate, altering the surface of the workpiece. Because of the impact and cutting effect of abrasives on the workpiece surface, the working surface will acquire varying roughness, improve mechanical characteristics, and increase fatigue durability. The impact of abrasives creates very small micropores on the working surface, enhancing the adhesion between the work and the coating and extending the coating’s useful life.
The following are the primary functions of sandblasting:
Sandblasting can remove dirt on the workpiece surface, such as rust skin, and generate a rough surface on the workpiece surface, which improves the adherence of plastic powder and paint film.
The burr on the surface of the machined workpiece can be eliminated by sandblasting to make the workpiece more appealing.
Sandblasting can remove oil and oxide scale from the surface of castings or heat-treated parts, improve the surface polish, and make the workpiece more attractive.
Powder coating is Electrostatic sprayed on the working surface using static electricity, and the powder is then baked at high temperatures to form a solid coating on the part surface.
To spray and atomize powder electrostatically, you’ll need an electrostatic generator to provide DC high voltage, a spray cannon, a power supply system, and a powder recovery system. The sprayed workpiece should be grounded to a positive pole, and the negative high voltage generated in the discharge needle gun connected to the powder outlet of the spray gun will produce corona discharge through the discharge needle. Under the influence of static electricity and compressed airflow, negatively charged powder particles reach the workpiece’s surface at this point.
The powder is uniformly adsorbed on the workpiece surface for a time without falling off due to electrostatic force attraction, and the workpiece is then placed in the curing furnace to flow flat and solidify, control the humidity or time, and finally form a tight, uniform, smooth, and dense coating that binds firmly to the workpiece.
Powder spraying smooths out the product’s surface and coats it with a coating that is acid, alkali, crashworthy, and wear resistant. Furthermore, the product can endure lengthy periods of exposure to strong UV radiation and acid rain without pulverization, discoloration, or shedding of the coating.
Surface brushed is a type of surface treatment that uses polishing materials to create beautiful lines on the workpiece’s surface.
The surface brushed technique is a type of surface-treatment technology that is used to create decorative surfaces using wire-brushed material for metal stainless steel aluminum surfaces. It can make the surface of a metal matte finish fine-brushed luster product vividly display each small silk mark. Because wire-brushed surface treatment may give materials a new texture and make items more attractive, pull wire processing is becoming increasingly popular.
Wire brushed processing has no common classification or title. It is usually classified into straight wire and silk yarn based on surface effects. Silk thread is also known as silk thread, and silk yarn is known as snow pattern.
Galvanolysis is used in electroplating to plate other metals on workpieces. It attaches component surfaces to metal films by electrolysis, with the goal of reducing metal oxidation (corrosion), improving abrasion resistance, conductivity, reflective resistance, corrosion resistance (like copper sulfate), and improving aesthetics, among other things.
Anode plating workpiece, cathode coating metal cations are reduced to produce coating surfaces on the workpiece surface by electroplating metal or other insoluble materials. An electroplating solution containing plating metal cations should be used as a plating solution to keep the concentration of metal cations unchanged and to eliminate interference from other cations, as well as to make plating homogeneity and firm.
Methods of surface treatment
The following are some of the most regularly utilized surface treatments. The table shows surface treatments that use electricity and require a separate power source in red characters.
Category | Process | Explanation |
---|---|---|
Cleaning | Cleaning | Cleaning is a process to remove oil, surface oxides, burrs and foreign substances. It can prolong the life of painting and plating. Among the cleaning processes, blasting and honing use abrasives and grinding wheels, respectively, so these processes can be said to be both cleaning and polishing. |
Blasting | ||
Honing | ||
Polishing | Mechanical polishing | Polishing the surface to make it smooth. While polishing is generally associated with rubbing with a grinding stone or brush, chemical or electropolishing slightly dissolves the surface to make it smooth. Electropolishing uses electrolysis to dissolve the surface of the part in a solution. |
Chemical polishing | ||
Electropolishing | ||
Painting | Spray painting | This is the process of adding paint to a surface. This is done to improve corrosion resistance and decorative properties. Electrostatic coating is a type of coating in which the paint is charged and adheres efficiently with the force of static electricity. Powder coating is also a type of electrostatic coating. Electrodeposition coating is a method of depositing paint on the surface of a part by electrolysis of a solution of special paint and is used for the base of automobile bodies. |
Electrostatic coating (Electrostatic painting) | ||
Electrodeposition coating | ||
Plating | Electroplating (electrolytic plating) | Plating is the process of covering the surface of a component with a thin film of another metal. Electroplating is a method of depositing a coating on the surface of a part by electrolyzing a solution. This is mainly done on metals such as iron to provide corrosion resistance and decorative properties. In some cases, plating is applied to the surface of plastics for decorative purposes, but the number of such applications has been decreasing in recent years due to improvements in coating technology. |
Chemical plating | ||
Hot dip coating | ||
Heat treatment | Surface quenching | This is a treatment that hardens the surface of metals to improve their resistance to wear and fatigue. By heating and cooling the metal, the structure of the metal surface is changed, making it harder. In surface quenching, there is a method called high-frequency quenching, in which a high-frequency current is applied to a coil, heating the part in the manner of a so-called induction heater. |
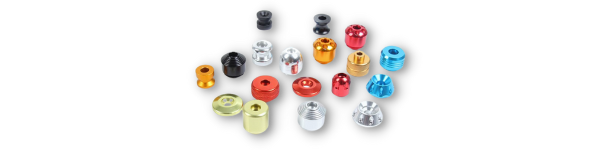