What is our precision CNC machining parts service?
Zümre Makina manages 50 machines with network and self-investment, and the precision CNC machining service provided significantly shortens the production cycle, reduces the cost of parts, and many precision CNC lathes and milling machines. The parts were produced quickly. We have a large number of custom processing partners and have passed ISO9001: 2015 certification. Zumre Makina can use over 40 different materials to process parts, makes the surface finish of products, and perform a variety of surface finished .
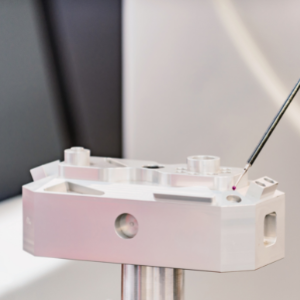
3/5 Axis CNC Machining
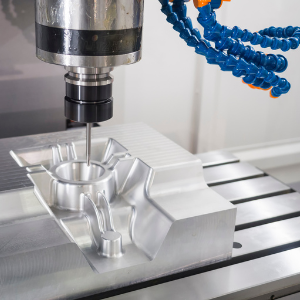
CNC Machining
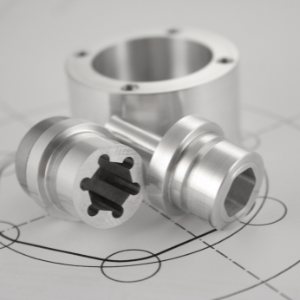
CNC Turning
How do we start precision CNC machining parts service?
Zümre Makina is your CNC manufacturing partner for prototyping and mass production of CNC machined parts and CNC turned parts. Our concept is to make the best custom CNC machining parts from the beginning!
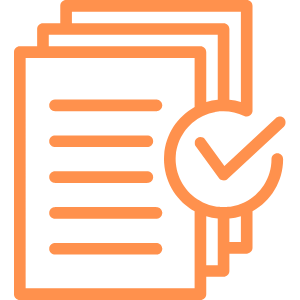
Free assessment of precision CNC machining
Send your idea or 3D or CAD files and we'll get your project started right away for free evaluation. Our goal is to complete a quality and cost-effective plan for your parts within 30 minutes.
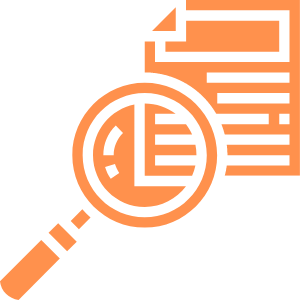
DFM Feedback
Before we start producing custom machined components, we'll make a DFM analysis and develop a process control plan for all quality risk points. Our engineers will develop DFM risk-based program and then organize tools and cuttings to ensure the consistency of partial quality.
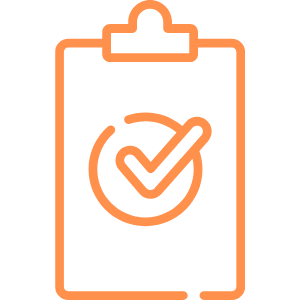
Production and Quanlity control
During the precision machined parts production process, our QC engineers will conduct patrol inspections based on the engineering drawings, and follow certain test methods and frequencies to ensure that the quality meets the requirements of the drawings (appearance, dimensions, tolerances).
How does a CNC machine work?
CNC machining begins with a computer, where designers use CAD (Computer-aided Build) software to design a product. After that, the digital portion is translated into a format that a CNC machine can understand.
The CNC machine receives instructions in the form of “G-Code,” after which it can begin cutting.
To keep a block of material — known as the “workpiece” — in position, most CNC machines incorporate a “worktable” and a work holding device. Depending on the machine’s design, the worktable may or may not move.
The cutting tool makes contact with the workpiece as machining begins, cutting away layers of material. The tool and/or workpiece are moved and/or swiftly rotated in accordance with G-Code instructions, ensuring that cuts are performed in precisely the appropriate areas until the part is complete.
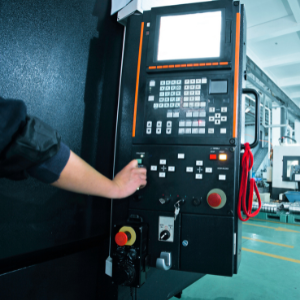
How to choose materials and compare with national standards of various countries, so as to find precision cnc machining parts suppliers, or to facilitate communication during design?
We have prepared 40 kinds of material inventory in our partner companies warehouses to ensure that customers’ prototypes and small batch precision machining parts and mass production are completed within 24 hours.Some of our materials are approved by IMDS.
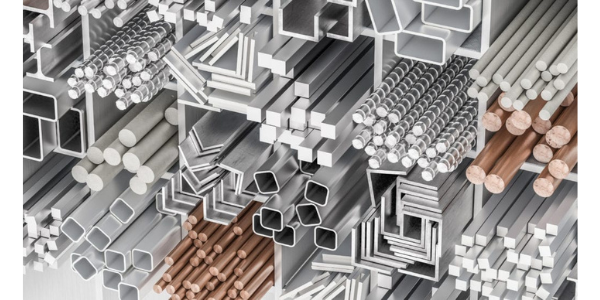
Material properties | Material model | American Standard (ASTM) | German standard (DIN) | Japanese Standard (JIS) | Chinese Standard (GB) | British Standard(BS) |
---|---|---|---|---|---|---|
Aluminum | Aluminum6061 | 6061 | AlMglSiCu | A6061 | LD30 | H20 |
Aluminum7075 | 7075 | AlZnMgCu1.5 | A7075 | LC9 | L95 | |
Aluminum2014 | 2014 | AlCuSiMg | A2014 | LD10 | 2014 | |
Aluminum2024 | 2024 | AlCuMg2 | A2024 | LY12 | GB-24S | |
Aluminum5052 | 5052 | AlMglSi0.5 | A5052 | LD31 | H19 | |
Aluminum6063 | 6063 | ALMg2.5 | A6063 | LF2 | NS4 | |
Aluminum1060 | 1060 | – | A1060 | L2 | – | |
Aluminum1070 | 1070 | A199.7 | A1070 | L1 | – | |
Aluminum1080 | 1080 | A199.8 | A1080 | LG1 | 1A | |
Stainless steel | Stainless steel 304L | 304L | X2CrNi19-11 | SUS304L | 022Cr19Ni10 | 403S17 |
Stainless steel 316L | 316L | X7Cr14 | SUS316L | 022Cr17Ni12Mo2 | 416S21 | |
Stainless steel 301 | 301 | X5CrNi17-7 | SUS301 | 12Cr17Ni7 | – | |
Stainless steel 304 | 304 | X5CrNi18-10 | SUS304 | 06Cr19Ni10 | – | |
tainless steel 430 | 430 | X6Cr17 | SUS430 | 10Cr17 | – | |
Brass | CuZn38Pb2 | C37700 | CuZn39Pb2 | C3771 | HPb59-1 | CW612N |
CuZn39Pb3 | C38500 | CuZn39Pb3 | C3603 | HPb58 | CW614N | |
CuZn36Pb3 | C38600 | CuZn36Pb3 | C3601 | HPb63 | CW603N | |
Copper | C10200 | OF-Cu | C1020 | T1 | C101 | |
C11000 | SE-Cu | C1100 | T1 | C101 | ||
Steel | Mild steel 1015 | 1015 | C15 | S15C | 15 | 095M15 |
Mild steel 1045 | 1045 | C45 | S45C | 45 | 080M46 | |
Mild steel 1020 | 1020 | C22 | S20C | 20 | 050A20 | |
Titanium | Titanium Grade 1 | GR1 | – | TP270 | TA1 | – |
Titanium Grade 2 | GR2 | – | TP340 | TA2 | – | |
Titanium Grade 4 | GR4 | – | TP550 | TA4 | – | |
Plastic | PTFE | PTFE | PTFE | PTFE | PTFE | PTFE |
PEEK | PEEK | PEEK | PEEK | PEEK | PEEK | |
NYLON | NYLON | NYLON | NYLON | NYLON | NYLON |
How do we make every precision CNC machined part have a consistent quality during the production process?
Claim | Quality record |
DFM identifies key dimensions | DFM report |
Reduce customer drawing tolerances and issue in-plant engineering | Drawings |
Identify key size | Procedur esheet |
First article inspection before delivery | First record |
Line inspection during production | Inspectio record |
Process CPK control | SPC report |
Sampling inspection of products in process | Shipmentin spection record |
Shipment inspection | Full size report |
Reliability test | Material proof |
Environmental protection requirements guarantee | ROHS report |
How do we make every precision CNC machined part have a consistent quality during the production process?
With our partner companies, we can get your CNC machiend parts surface finished.
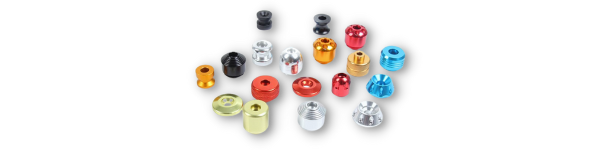
Part material | Surface treatment method | Principle details | Function and standard |
---|---|---|---|
Aluminum | Clean Anodized | Anodizing can enhance the wear and corrosion resistance of the surface of the precision CNC machining part, and increase the surface hardness. | Hardness can reach 5UM-60UM |
Color Anodized | Rich colors increase brand value | According to customer requirements, multi-color effects can be produced | |
Powder Coating | Perform color matching according to Pantone and labor color card ral9016. | High temperature resistance, wear resistance and additional force | |
Bead blasted | Guarantee the statistical precision CNC machining parts surface effect,Can be implemented in accordance with Apple’s surface grade requirements. | According to SSPC—SP7 level execution | |
Brushing | Use the surface to maintain uniform rules and beautiful lines. | Can reach between Ra1.2UM-Ra40UM | |
Polishing | Use a grinding wheel or cloth wheel and wax to remove to maintain the surface finish. | Can reach between Ra1.2UM-Ra40UM | |
Stainless steel | Polishing | Use a grinding wheel or cloth wheel and wax to remove to maintain the surface finish. | Can reach between Ra0.6UM-Ra1.6UM |
Passivating Sandblasting | The effect of passivated fine sand, the surface has corrosion resistance. | According to SSPC—SP7 level execution | |
PVD | CrN. TiN. TiAlCN. TiCN. TiAlN, etc. are plated on the surface to make the surface clear and beautiful. | Abrasion resistance, high cleanliness | |
Steel | Polishing | Use a grinding wheel or cloth wheel and wax to remove to maintain the surface finish. | Can reach between Ra0.6UM-Ra1.6UM |
Polishing, Plating Nickel/Chrome/Zinc | The process of using electrolysis to attach a metal film to the surface of metal or other materials to prevent metal oxidation (such as rust), improve wear resistance, electrical conductivity, light reflectivity, corrosion resistance (copper sulfate, etc.) and Enhance beauty and other functions. | According to ASTM B578-1987 (R2015) standard | |
Heat treatment | Metal heat treatment is a process that heats, heats, and cools a metal precision CNC machining in a certain medium, and controls its performance by changing the surface or internal structure of the metal material. | According to the standard BAC5617 execution | |
Powder coated | The spraying effect of powder spraying is in terms of mechanical strength, adhesion, corrosion resistance, aging resistance, etc. | Standard Guide for Testing Coating Powders and Powder Coatings in accordance with ASTM D 3451-2006 | |
Brass | Plating Nickel | There are two processes of electroless nickel plating and electrolytic nickel plating, one is for conductive, the other is for decorative protection. | 1. Improve anti-corrosion fatigue life. 2. Improve the service life of wear |
Chrome | The process of using electrolysis to attach a metal custom CNC machining parts film to the surface of a metal or other material. | Improve precision CNC machining parts wear resistance, reflectivity, corrosion resistance (copper sulfate, etc.) and enhance aesthetics | |
Zinc | The purpose of cold galvanizing is mainly to prevent rust, and hot galvanizing has high anti-corrosion and anti-rust effect. | ASTM B695-2000 and military C-81562 mechanical galvanizing technical standards | |
PVD | Before the copper is used for PVD, we must first polish and chrome the copper, and then perform PVD, the effect is even more beautiful than the ordinary electroplated surface. | Wear-resistant, high clarity, can be made in a variety of colors |